The Leader In Compressed Air Innovation®
Custom OEM Air Compressor Solutions
Custom OEM solutions bring the reliability of a VMAC rotary screw air compressor system to your industrial engine applications. We manufacture continuous duty rotary screw air compressor systems ranging from 15-150 CFM for the most common industrial engines.
VMAC air compressors are used by OEMs across the globe, with many partnerships in North America and Europe. We’re proud of the quality work we do with our partner OEMs, including Caterpillar, Cummins, DEUTZ, Finning, Ford, John Deere, Kubota, Lincoln Electric, New Flyer, and many more.
Contact us online, or read more below to learn about VMAC’s custom solutions.
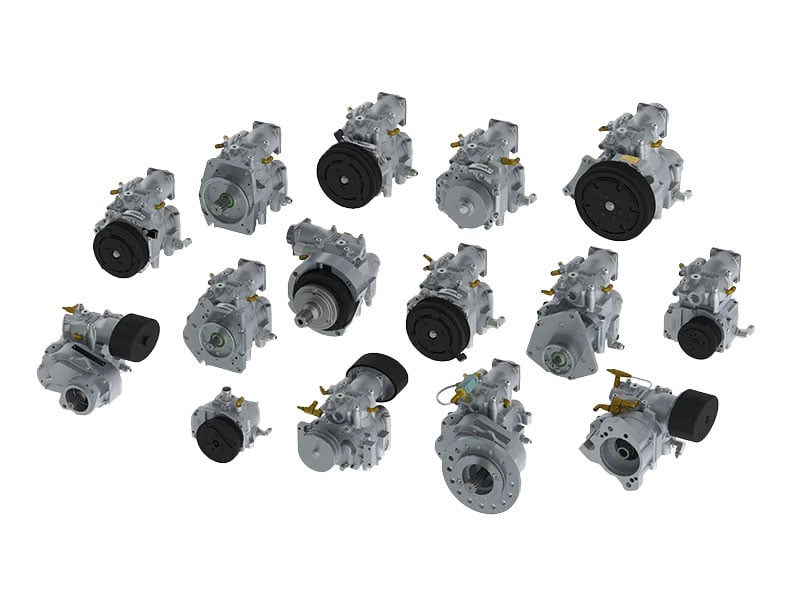
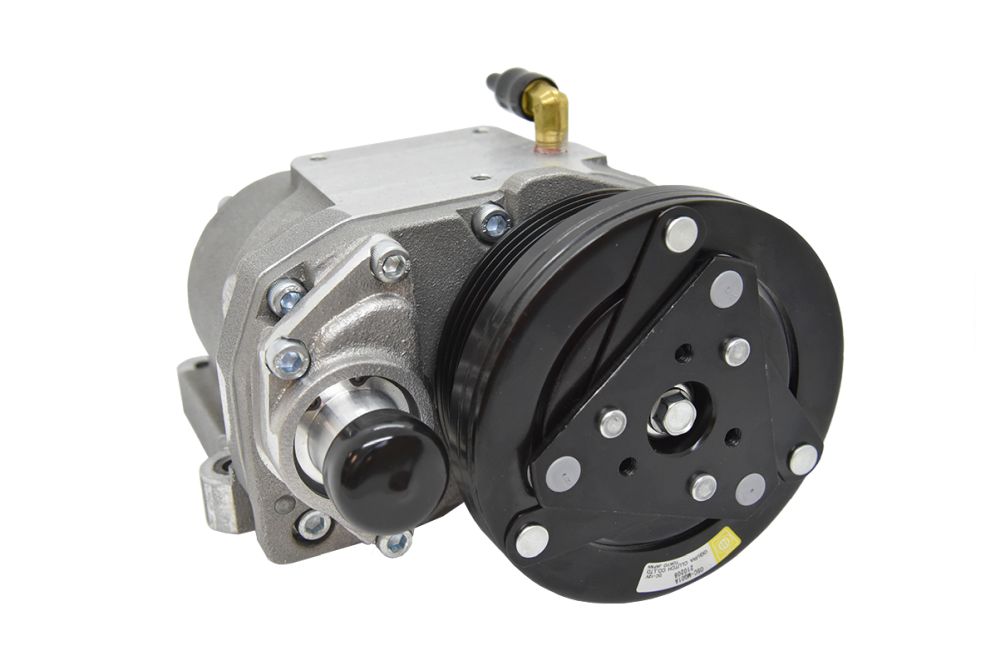
Belt Drive Air Compressors
Browse VMAC OEM compressors and components, offering 15-150 CFM air output.
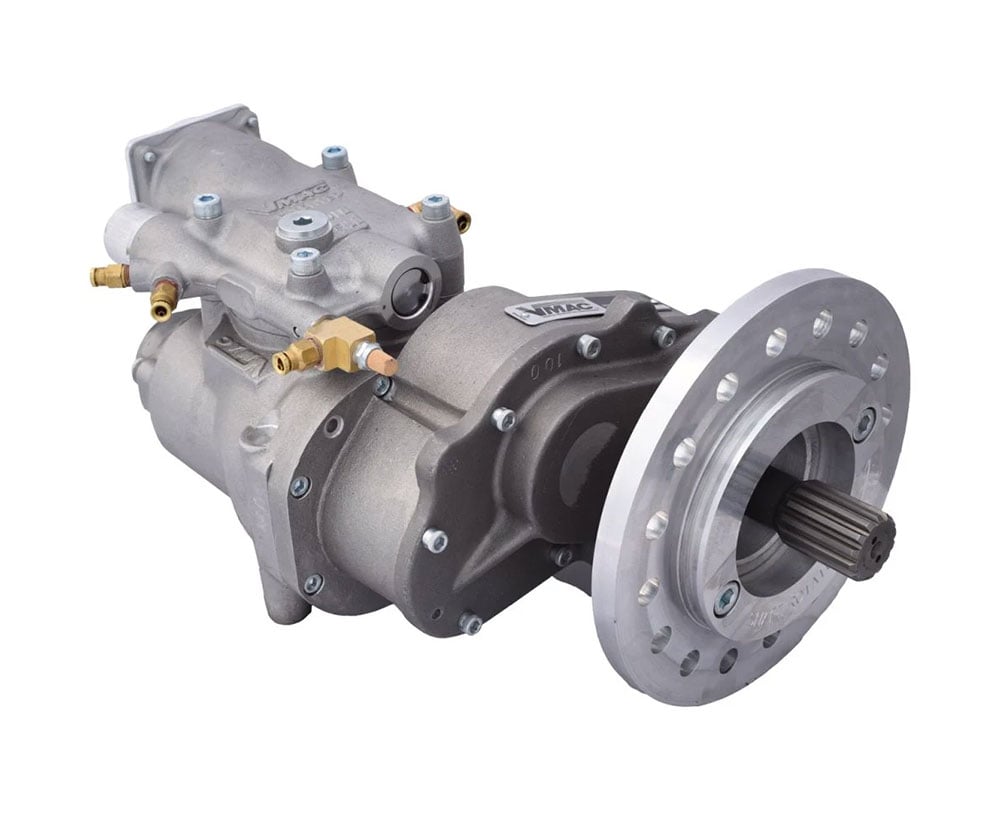
Spline Drive Compressors
These direct drive rotary screw air compressors feature a lightweight, aluminum design and operate at 100% duty cycle.
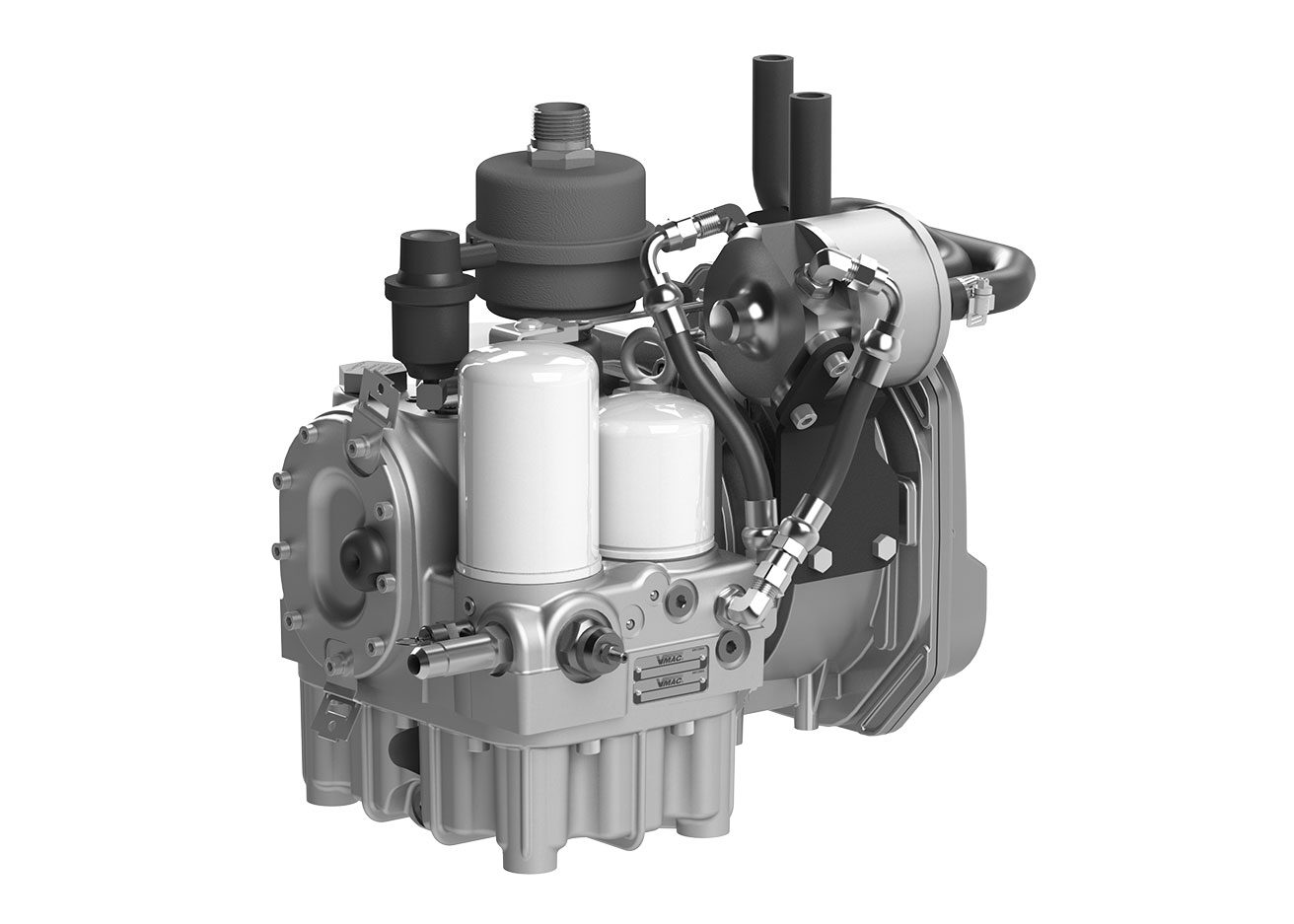
Electric Air Brake Compressors
Discover 10-20 CFM electric air brake compressors for transit buses, school buses, and Class 8 trucks.
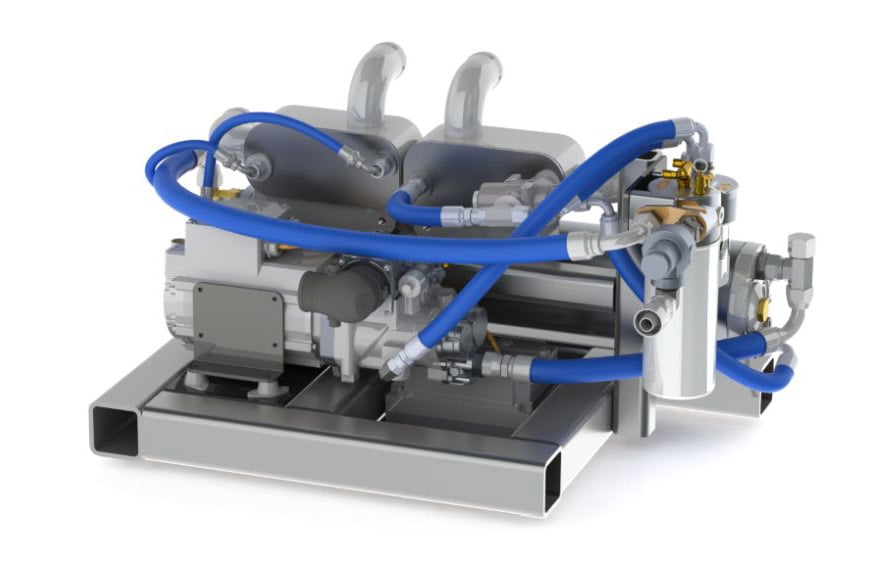
Electric Air Compressors
VMAC works with our partner OEMs to develop 20-130 CFM custom electric air compressor packages to their specifications with 200-1,000 Volt applications.
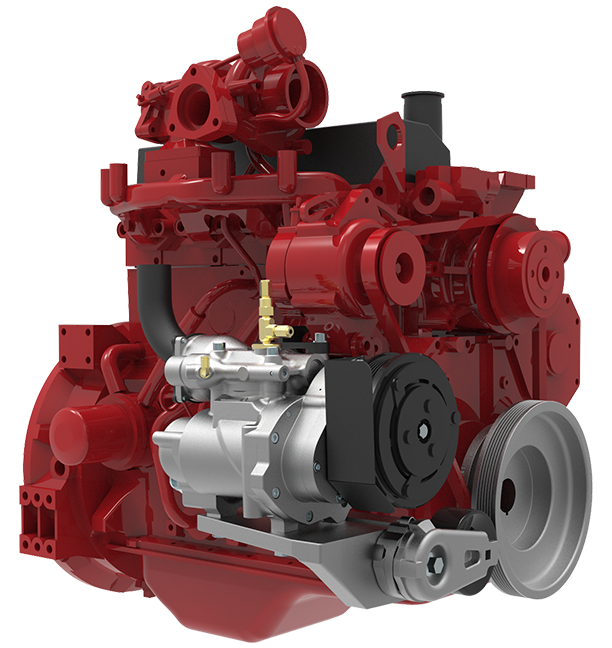
OEM Industrial Engine Applications
VMAC has over 25 years of experience developing custom mounting kits for industrial engines.
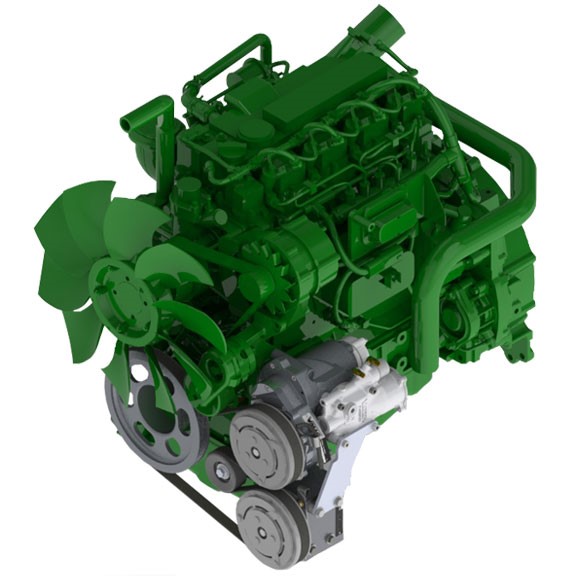
OEM Industries & Applications
VMAC designs OEM air compressors for a variety of the most challenging applications.
Why Choose VMAC
VMAC designs and manufactures the most innovative custom rotary screw air compressors available. Engineered and manufactured in Canada, VMAC air compressor systems and components are custom built to suit your specific application. Find out why many top companies, including Caterpillar, Cummins, DEUTZ, Finning, Ford, John Deere, Kubota, Lincoln Electric, and New Flyer trust VMAC for their air compressor solutions.
Higher Output Than Reciprocating Air Compressors
Most industrial engines have a factory option for a reciprocating compressor designed for intermittent duty applications, but for industries like dust collecting, spray foam applicators, prime assist water pumps, road patching and air arc gouging, a more robust rotary screw compressor is required. VMAC OEM custom rotary screw air compressors are powerful, delivering the CFM you need at 100% duty cycle and allowing you to get jobs done faster, improving productivity.
Compact & Lightweight
VMAC air compressors are designed to be compact and lightweight, conserving space and weight on any platform. The compact size of VMAC air compressors enables them to fit in tight spaces. Lightweight equipment is more mobile and frees up weight, allowing you to add more equipment, carry more materials, or save on fuel costs.
Technical Support
VMAC’s highly trained technical support team is available to help by phone and email. With VMAC’s superior technical support on hand, you’ll be able to get the answers you need, and back to work faster.